Compliance / Risk management
Compliance
As described in the Mitsubishi Steel Group Code of Conduct, the Group carries out business activities in compliance with laws, regulations, and societal norms.
Enhancement of the compliance structure
Based on the Basic Regulations on Compliance, which applies to all Group companies, the Group strives to enhance its compliance structure by appointing individuals responsible for compliance at individual facilities and subsidiaries and cooperating with a Chief Compliance Officer (director in charge of Risk Management Office). As the section in charge of overseeing compliance, the Risk Management Office exchanges information regularly with the individuals responsible for compliance and also drafts and implements compliance measures.
Compliance initiatives
Response to serious compliance risks
We are currently studying and implementing the following measures to address serious compliance risks, including risks posed by corruption, cartels, and quality misrepresentation. These measures are intended to prevent compliance violations in Japan and overseas.
- Establishing and implementing regulations on compliance with the Antimonopoly Act
- Establishing and implementing guidelines and response flowcharts to prevent corruption
- Establishing and implementing quality audit regulations and quality audit manuals (internal audits by quality sections)
Compliance training
The Group is currently enhancing its compliance training programs. Training efforts include reviews of practical case studies, preparation of content and teaching materials tailored to specific employee levels from executives to ordinary employees, discussions, and other activities. Examples of training programs implemented to date are given below.
- Executive compliance training (led by an outside instructor)
- Training for managers on harassment
- Training for individuals responsible for compliance and for Sales Division general managers on prevention of cartels
- Level-specific training on the Detailed Rules for Mitsubishi Steel Manufacturing Group Corporate Code of Conduct (for facilities in Japan, including subsidiaries)
- Training on prevention of quality misrepresentation (for quality control sections at manufacturing facilities in Japan)
We plan to sustain efforts to raise awareness of compliance issues and to ensure thorough understanding of compliance issues among all Group employees.
Review of the state of operation of the compliance Structure
To enhance oversight of the compliance structure, matters related to the state of its operation are reviewed and submitted annually to the Board of Directors.
Results of the review conducted in FY2021 verified that the Company's compliance structure is operated appropriately.
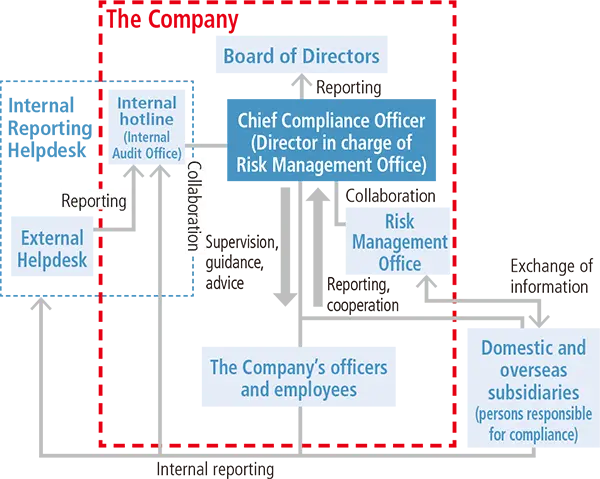
Internal whistleblowing system
We have established a structure whereby Group employees, who observe violations of laws or regulations, inappropriate actions, or other potential issues but feel uncomfortable raising these issues with workplace personnel, can report to or consult with internal or external contacts outside the workplace. Whistleblowing reports and consultations are accepted by telephone, email, fax, post, and other written means, as well as in person. Reports can also be submitted anonymously. Our overseas facilities also continue to adopt internal whistleblowing systems. To date, these systems have been adopted at subsidiaries in Thailand, China, the Philippines, and India.
Since FY2023, we have strived to identify and resolve compliance violations and similar issues quickly by including in compliance training descriptions of this system, such as the structures for responding to reports and protecting whistleblowers, and encouraging use of the system.
FY2020 | FY2021 | FY2022 |
---|---|---|
5 | 3 | 5 |
- *Incudes domestic and overseas subsidiaries
Cutting off relations with antisocial forces
As stated in the "Mitsubishi Steel Group's Business Conduct Guidelines," our Group is firmly opposed to antisocial forces and has established that we will have no relations with them. Based on this, we have concluded a memorandum with our business partners regarding the exclusion of antisocial forces. In addition, as part of our employee education, we strive to comply with the "Mitsubishi Steel Group's Business Conduct Guidelines," including instructing employees to cut off relations with antisocial forces and to deal firmly with threats and unreasonable demands without yielding.
Risk management
The Group carries out appropriate ascertaining and management of risks to minimize losses and maximize gains as we fulfill our social responsibilities through sustained growth.
Development of the risk management structure
The Group established the Investment and Credit Committee, led by the Corporate Planning Division, to contribute to management decisions through close examination of business plans and risks from a neutral perspective on issues potentially entailing risks of business losses.
We have also established a Risk Management Committee, led by the Chief Risk Officer (CRO), whose members consist of individuals responsible from the Control & Administration Unit. The purpose of the committee is to manage risks effectively in governance, compliance, and other aspects at domestic and overseas facilities. The committee seeks to identify major risks and draft countermeasures to address these risks.
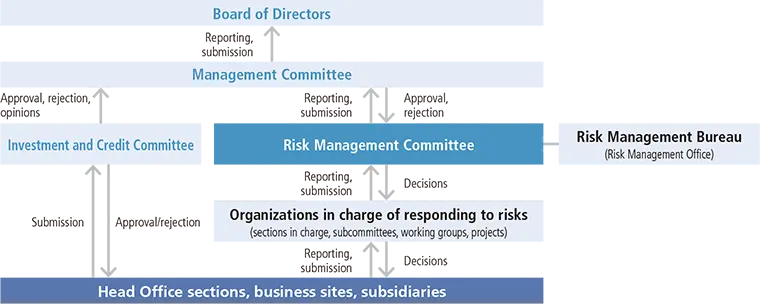
Information security measures
Information security risks continue to proliferate around the world. To ensure preparedness for such risks, based on the our Corporate Philosophy and the Mitsubishi Steel Group Code of Conduct, the Group has established a Basic Policy for Information Security, as well as associated regulations and associated information security management structures.
These measures focus on establishing an Information Security Committee whose members consist of the individuals responsible from the Company's sections and the Group companies. The committee is charged with implementing measures to prevent information leaks, unauthorized alteration or destruction of data and ensuring swift response to major incidents. The committee oversees information security across the entire Group.
We also provide continual training and education on information security for Group employees and perform internal audits to evaluate related aspects such as the state of retention and control of confidential or sensitive information, thereby raising awareness of the significance of information security throughout the organization. In particular, given globally increasing cyber attacks in recent years, we have enhanced training and education for all employees on targeted email attacks, performing periodic Computer Security Incident Response Team (CSIRT) drills for potential incidents, and also taken out cyber risk insurance to ensure preparedness for any eventuality. These are part of efforts to strengthen and enhance information security.
Countermeasures against quality misrepresentation
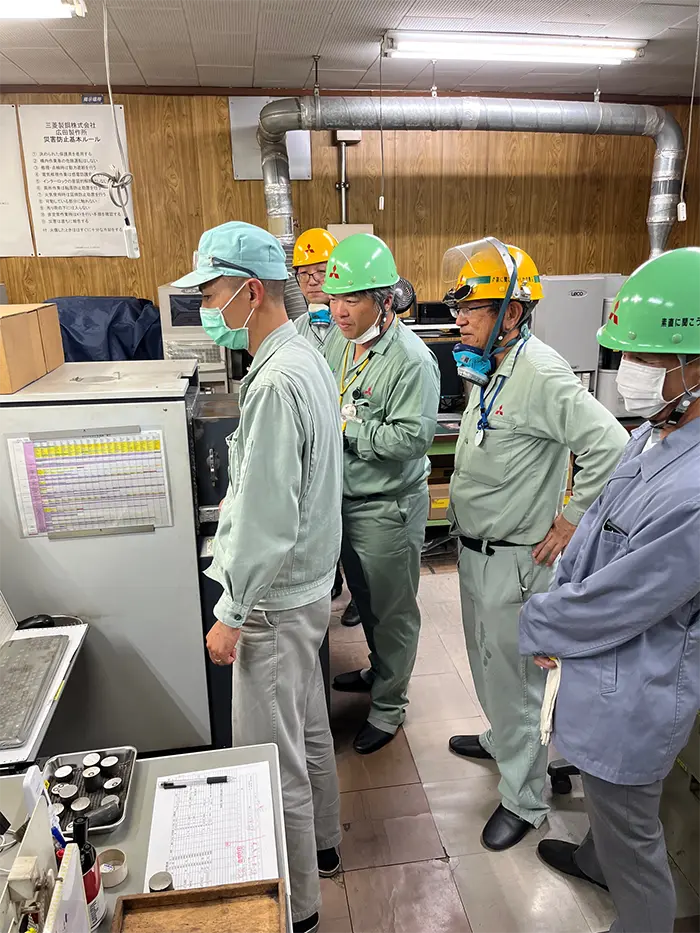
The Group has established quality assurance structures at each production facility and strives to enhance these structures to deliver quality that keeps customers satisfied. As part of these efforts, since FY2020 quality control sections have continued to perform internal audits that aim to prevent unauthorized alteration of quality data and quality misrepresentations under the leadership of the Risk Management Office.
These internal audits check for the three main contributing factors to improprieties: motive, opportunity, and justification. The audits strive to prevent unauthorized alteration of quality data and quality misrepresentations before they occur.
With the goal of heightening awareness of the importance of quality controls, we provide periodic compliance training for our employees in quality control sections. In addition, we are currently making progress on automating inspection systems and developing related automation technologies.
Business continuity planning measures
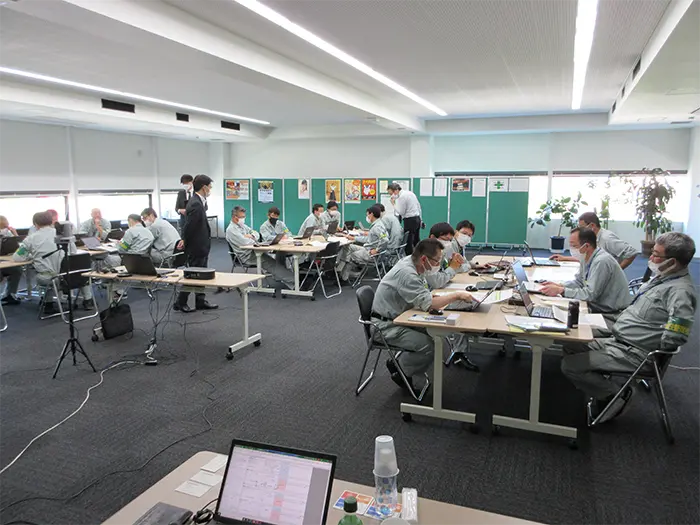
To enable the rapid collection of information and coordinated guidance in response to severe threats to business operations such as disasters, accidents, and infectious diseases, the Group has established guidelines for establishing emergency task forces and maintains a business continuity plan (BCP) to enable each section, business site, and subsidiary to respond and achieve recovery without delay. We prepared BCPs on responding to major earthquakes in FY2020 and on responding to infectious diseases in FY2021, and we are preparing BCPs on responding to storms and flooding at sites expected to be at risk of typhoons.
Each business site carries out periodic BCP training to promote awareness of the BCP and BCP drills to verify and revise the BCP previously formulated.
We will continue to perform drills to strengthen our capacity to respond to risks and improve the BCP, thereby enhancing our business continuity capabilities.
Overseas crisis management measures
We have taken measures to ensure that expatriate staff, accompanying families, and business travelers living in environments completely different from the safe and sanitary conditions in Japan can live overseas with peace of mind in case of emergencies.
In collaboration with a specialist company for overseas crisis management, we have a system in place to provide advice and assistance in Japanese 24/7, 365 days a year, in terms of medical care and security (crime, disasters, etc.), no matter where in the world they are.
In addition, whenever there is cautionary information due to climate or protest activities, we share information between the headquarters and overseas bases, and value international communication on a daily basis.
Fire prevention measures
As part of its safety measures, each manufacturing facility in the Group strives to enhance fire prevention measures. Together with regular follow-up on the Groupwide fire risk checks launched two years ago, we are taking action to prevent fires by deploying Groupwide measures based on the lessons of past fires.
We are also promoting fire prevention awareness through continual monitoring, improvements, and periodic patrols to highlight fire risks.
Lifesaving initiatives
Among its disaster prevention measures, the Company provides regular lifesaving courses for employees at the Head Office. Lifesaving has been a particular focus especially in the past few years, for example by adopting a basic goal of having all employees at the Head Office earn lifesaving qualifications and encouraging those already qualified to participate in repeat training once every three years to keep their qualifications valid. These courses continued even during the COVID-19 pandemic, with appropriate safety measures. As a result, a total of more than 180 persons (including those taking repeat training) completed the course during the six years since 2017, and the Tokyo Fire Department presented us with a letter of thanks reflecting its high regard for our contributions to lifesaving activities in the community.
We will continue these regular courses to improve employees' knowledge and skills regarding lifesaving.
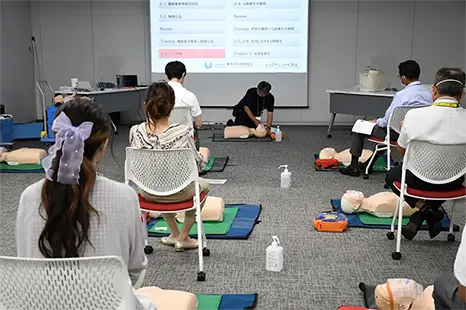

Privacy Policy
The Mitsubishi Steel Personal Information Protection Policy is available on our website.
https://www.mitsubishisteel.co.jp/english/privacy/index.html