Efforts to lessen environmental impact
Considering eco-friendly products to be an important topic, we develop and sell products to reduce environmental impact not just within our own organization but also at customers and across society as a whole.
Renewable energy (machinery for offshore wind power generation)
In one effort to contribute to offshore wind power generation, Mitsubishi Steel Group member company Mitsubishi Nagasaki Machinery Mfg. Co., Ltd. manufactures products for offshore wind turbines and the machine and equipment needed to install them. We are also focusing on expansion and enhancement of plant facilities to increase production capacity for offshore wind power-related products.
In addition, efforts at Mitsubishi Steel Muroran Inc. include earning Transportation and Power Generation (TPG) accreditation as a supplier of steel materials for use in offshore wind power equipment parts. Leveraging strengths of the Group's ability to handle large-scale products, we will contribute to development of a domestic supply chain for offshore wind power in Japan.
As another part of its efforts related to offshore wind power generation to achieve a carbon-zero society, Mitsubishi Steel has become a member of the Muroran Offshore Wind Industry Promotion Association (MOPA), which seeks to attract businesses related to the offshore wind power industry to the city of Muroran, Hokkaido, and to stimulate local industry. Mitsubishi Steel Adviser Hiroshi Sekine was appointed MOPA chairperson in November 2021.
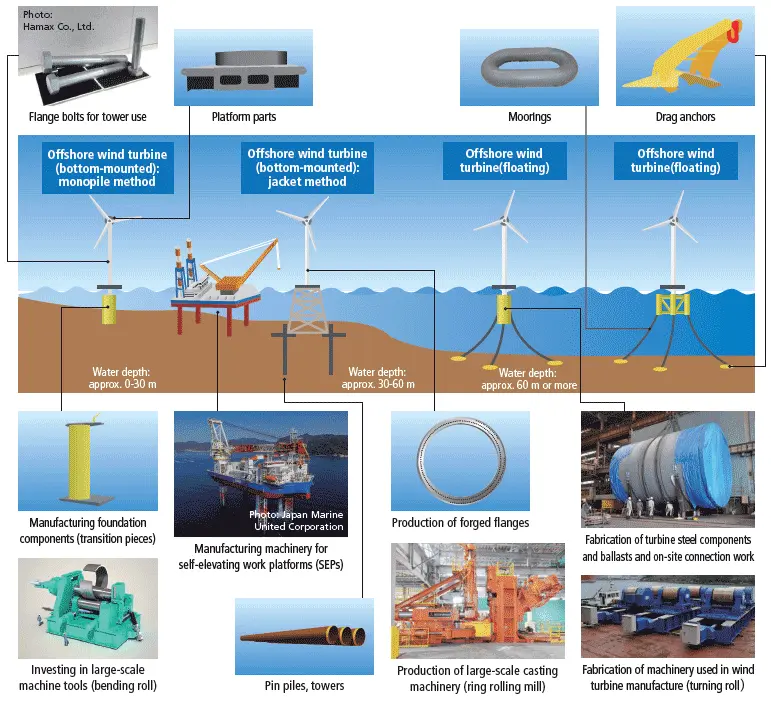
Efforts toward a circular economy
Mitsubishi Steel Group member company Mitsubishi Nagasaki Machinery Mfg. Co., Ltd. produces various types of sorting machinery to help realize a circular economy.
It has developed a sorting line that combines various magnetic separators and optical color separators to segregate and recover with high precision various recyclable resources from mixed scrap, including resources from waste home electronics and waste electric motors.
By recovering copper with high precision and efficiency from urban mining, this system will contribute to mitigating future shortages of copper, essential to the electric motors used in electric vehicles, which are expected to see growing use in the future.
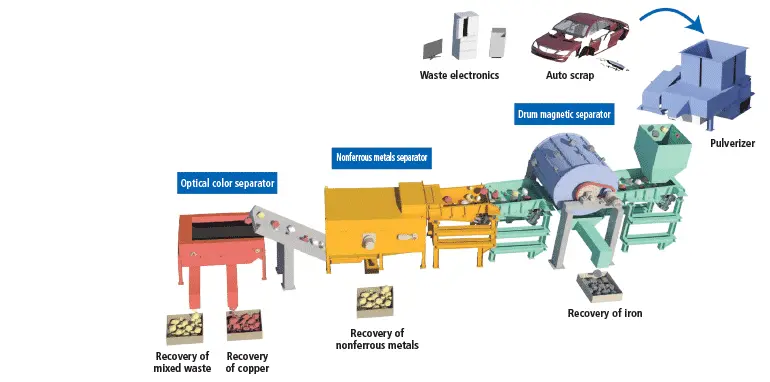
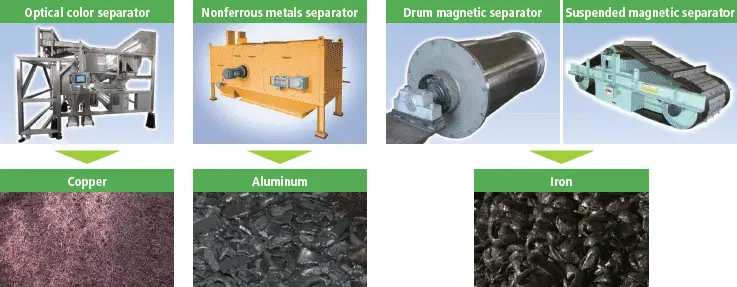
Mitsubishi Nagasaki Machinery Mfg. exhibited its separators in the 32nd New Environmental Exposition 2023, held May 24–26 at Tokyo Big Sight. The New Environmental Exposition is a trade show for the environmental business that attracts manufacturers of environmental equipment not just from across Japan but from Asia, Europe, and other overseas markets. It is one of the largest exhibitions of environmental equipment in Japan. Over the three days of the event, more than 1,000 attendees visited the Mitsubishi Nagasaki Machinery Mfg. booth— an indicator of the high level of interest in the metals recycling field in efforts toward a circular economy.
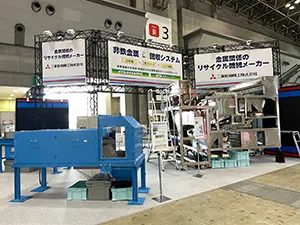
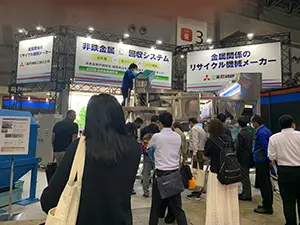
Environmentally-friendly Material Development
Some themes are being promoted through industry-academia collaboration.
Omission of forging and heat treatment processes

Development of materials for lithium-ion batteries
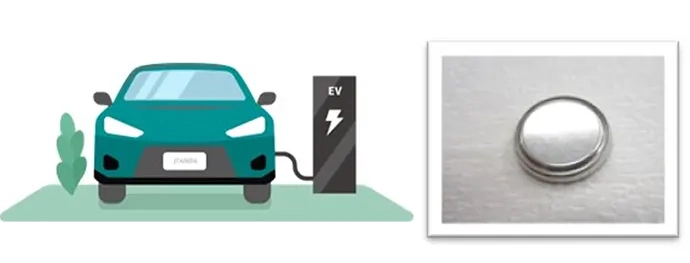
Lightweighting automobiles | FRP springs
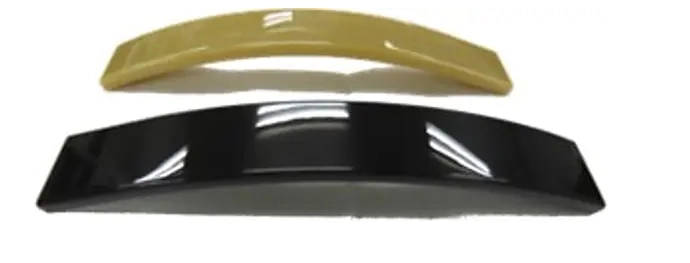
Development of powders for environmentally friendly products
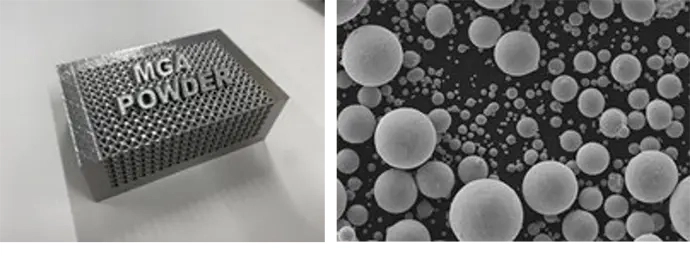
For more details on research and development, please refer to the "Technology Development Center."
Non-heated steels and steels for direct quenching after casting
Motor vehicles and construction machinery use numerous forged parts. Normally, forged parts are cooled to room temperature after hot forging (heating to approx. 1,200°C), then heated once again to temperatures of 800°C or more for quenching and tempering.
Using the following materials, we are helping customers reduce their CO2 emissions while conserving energy and simplifying processes.

- 1Non-heated steels
- Ideal for achieving a wide range of strengths, these steels are hardened through a process involving the deposition of carbide and nitride elements.
- These materials make it possible to secure the designated mechanical properties (strength and toughness) by controlling the speed of cooling after hot forging. They do not require quenching and tempering through thermal processing after hot forging.
- 2Steels for direct quenching after casting
- Quenching and tempering are essential for certain parts, since non-heated steels cannot meet the required specifications.
- We are developing materials that can be quenched immediately after forging.
The production of these materials applies residual heat from hot forging. - The appropriate combination of materials and forging conditions allows direct quenching after casting.
Making automotive springs lighter
- Coil springs
As a manufacturer who handles all processes from raw materials through final products, we draw on materials and process developments to make automotive springs lighter and thereby reduce automotive CO2 emissions.
Progress on the development of materials and processes has generated practical solutions involving steel developed in house ② + basic processes and standard steel + improved processes ②. These processes cut spring weight by about 20% compared to standard steel + basic processes.
We are moving forward with development efforts that combine materials development with process improvements. Our goal is to help reduce the environmental impact of motor vehicles by making automotive springs lighter.
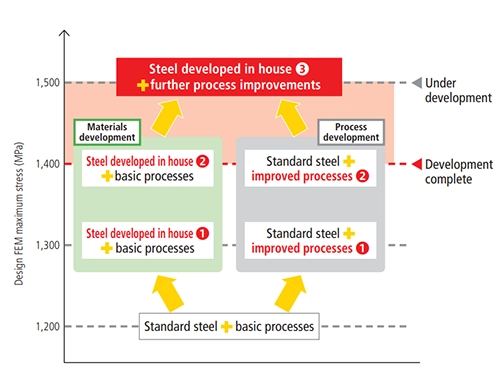
- Stabilizers
We improve durability and reduce the thickness of hollow stabilizers by applying proprietary interior surface treatment technologies.
We have reduced the weight of stabilizer products by more than 20%.We plan to begin mass production of these lightweight stabilizers no later than FY2025.
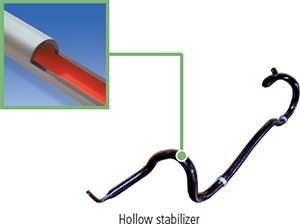
High-performance powders
Our soft magnetic metal powders are used to make the electronic components found in communication and control devices for smartphones, motor vehicles, and other products.
With expanding use of electric vehicles and self-driving vehicles, demand is expected to grow for soft magnetic powders for use in the inductors found in electronic control components.
We develop high-performance soft magnetic powders for automotive applications that require minimal energy loss. The powders are ideal for device miniaturization and high frequency components.
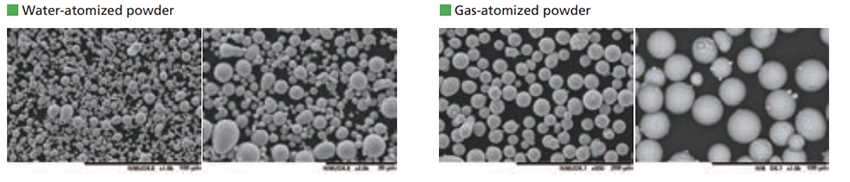